Holy Loch in summer. It would have been the midge that bit you Mikey.
THE midge? More like 60 billion.
LOL!!! We used to pressure wash the subs and the midges got blasted too when they came around. Unfortunately we had to paint the subs with a paint roller so the midges couldn't be spray painted, but they did get stuck in the paint, we just kept on rolling!!
BTW it takes 7 coats of paint from bare metal to finish coat to paint a US submarine!!! They are darker on the top half than the bottom half so they tend to blend into the area around them depending on whether you are looking up at them from below or down from above at them. The only part that gets treated differently is the sonar 'dome' and it gets VERY carefully spray painted to keep the paint as thin as possible. I was a welder, plumber, carpenter and professional firefighter and EVERYONE except the cooks had to 'water blast', ie pressure wash, the subs, those things are HUGE!!! Fortunately not every inch needed cleaning or painting but every 10 days we got a new one in during 'docking season' which was Spring thru Fall every year. Fortunately for me I was only there for one year, as a single guy that was all most of us did while married guys did at least 1 1/2 years and some did more.
I never got shocked soooo much in my life from welding as when I was there....the near daily rain and constant movement of things meant alot of repairs in the rain.We had wmetal walkways to walk above the water that pooled everywhere and they needed constant rewelding to the deck. Unfortunately that meant starting the weld above the water level and then trying to keep it going down under 2 to 3 inches of water to weld the walkway back to the deck again. Since it rained all the time there was never a break to fix it solid so it was always 'good enough' until the next time.
LOL!!! We used to pressure wash the subs and the midges got blasted too when they came around. Unfortunately we had to paint the subs with a paint roller so the midges couldn't be spray painted, but they did get stuck in the paint, we just kept on rolling!!
I once went camping and put the tent up, walked off for only 5 minutes, and found it covered in 950 flying ants - we counted them as we killed them, one by one by squishing them between our fingers. They were in some kind of "meet up" mode and didn't try to fly off.
mikey wrote:
BTW it takes 7 coats of paint from bare metal to finish coat to paint a US submarine!!! They are darker on the top half than the bottom half so they tend to blend into the area around them depending on whether you are looking up at them from below or down from above at them. The only part that gets treated differently is the sonar 'dome' and it gets VERY carefully spray painted to keep the paint as thin as possible. I was a welder, plumber, carpenter and professional firefighter and EVERYONE except the cooks had to 'water blast', ie pressure wash, the subs, those things are HUGE!!! Fortunately not every inch needed cleaning or painting but every 10 days we got a new one in during 'docking season' which was Spring thru Fall every year. Fortunately for me I was only there for one year, as a single guy that was all most of us did while married guys did at least 1 1/2 years and some did more.
Married guys get more work?
mikey wrote:
I never got shocked soooo much in my life from welding as when I was there....the near daily rain and constant movement of things meant alot of repairs in the rain.We had wmetal walkways to walk above the water that pooled everywhere and they needed constant rewelding to the deck. Unfortunately that meant starting the weld above the water level and then trying to keep it going down under 2 to 3 inches of water to weld the walkway back to the deck again. Since it rained all the time there was never a break to fix it solid so it was always 'good enough' until the next time.
Shocked? I thought welders were about 50 volts?
If this page takes an hour to load, reduce posts per page to 20 in your settings, then the tinpot 486 Einstein uses can handle it.
LOL!!! We used to pressure wash the subs and the midges got blasted too when they came around. Unfortunately we had to paint the subs with a paint roller so the midges couldn't be spray painted, but they did get stuck in the paint, we just kept on rolling!!
I once went camping and put the tent up, walked off for only 5 minutes, and found it covered in 950 flying ants - we counted them as we killed them, one by one by squishing them between our fingers. They were in some kind of "meet up" mode and didn't try to fly off.
mikey wrote:
BTW it takes 7 coats of paint from bare metal to finish coat to paint a US submarine!!! They are darker on the top half than the bottom half so they tend to blend into the area around them depending on whether you are looking up at them from below or down from above at them. The only part that gets treated differently is the sonar 'dome' and it gets VERY carefully spray painted to keep the paint as thin as possible. I was a welder, plumber, carpenter and professional firefighter and EVERYONE except the cooks had to 'water blast', ie pressure wash, the subs, those things are HUGE!!! Fortunately not every inch needed cleaning or painting but every 10 days we got a new one in during 'docking season' which was Spring thru Fall every year. Fortunately for me I was only there for one year, as a single guy that was all most of us did while married guys did at least 1 1/2 years and some did more.
Married guys get more work?
No their tour of duty rotation was longer because they were married, it's easier for a single guy to pack up and move than a guy with a wife and possibly kids.
mikey wrote:
I never got shocked soooo much in my life from welding as when I was there....the near daily rain and constant movement of things meant alot of repairs in the rain.We had wmetal walkways to walk above the water that pooled everywhere and they needed constant rewelding to the deck. Unfortunately that meant starting the weld above the water level and then trying to keep it going down under 2 to 3 inches of water to weld the walkway back to the deck again. Since it rained all the time there was never a break to fix it solid so it was always 'good enough' until the next time.
Shocked? I thought welders were about 50 volts?
No ours were 220/240 volts and then since we only used stick welders we changed the amps as needed with a dial on the front of the machines.
No ours were 220/240 volts and then since we only used stick welders we changed the amps as needed with a dial on the front of the machines.
The only one I used was a 3kW 240V input (plugged into a standard UK socket - you can't do that in America because of your 120V systems with less power!), but with a huge transformer to give out 50 volts at a higher amperage. Not sure if that was for safety or to provide a higher current. The best way to start a good arc is with DC, but I assume all welders rectify the AC from the mains.
I'm wondering if you're related to the Russian youtube people, Kreosan. I can't find the video now, but they were welding by simply using a direct connection from the mains! They ended up melting the plug. An African guy did it better, he put a bucket of salt water in series to limit the current, and he could adjust the current by changing the gap of the electrodes in the water.
If this page takes an hour to load, reduce posts per page to 20 in your settings, then the tinpot 486 Einstein uses can handle it.
No ours were 220/240 volts and then since we only used stick welders we changed the amps as needed with a dial on the front of the machines.
The only one I used was a 3kW 240V input (plugged into a standard UK socket - you can't do that in America because of your 120V systems with less power!), but with a huge transformer to give out 50 volts at a higher amperage. Not sure if that was for safety or to provide a higher current. The best way to start a good arc is with DC, but I assume all welders rectify the AC from the mains.
I'm wondering if you're related to the Russian youtube people, Kreosan. I can't find the video now, but they were welding by simply using a direct connection from the mains! They ended up melting the plug. An African guy did it better, he put a bucket of salt water in series to limit the current, and he could adjust the current by changing the gap of the electrodes in the water.
This page suggests it's up to 80 volts on the output when open circuit. The one I had I measured at about 50V. I can't remember if it was DC or AC. DC apparently gives you a stronger weld.
If this page takes an hour to load, reduce posts per page to 20 in your settings, then the tinpot 486 Einstein uses can handle it.
This page suggests it's up to 80 volts on the output when open circuit. The one I had I measured at about 50V. I can't remember if it was DC or AC. DC apparently gives you a stronger weld.
I have no clue but remember we had to crank it up the longer the leads were, ie being close to the welder itself or having to run wires 200 feet away and also based the material we were welding. Sometimes we cranked it waaaay down and used a 2nd welding rod as filler material when we had to fill a gap of several inches in cases where they didn't want to make a filler piece of metal. I had to fill a gap of more than 4 inches one night, yes I started after 4pm and didn't finish until after 7am the next morning. It was about 2 feet long going around a corner on an exhaust pipe. They needed to run the diesel engine starting at 8am so I did make it but it took FOREVER!!! AND it did NOT leak which was VERY important as the place where the engine was was under 40 feet of water in a pontoon with people in it when it ran. The engine ran the pumps to pump the water out of the 'wingwalls' when we went down to let the subs etc in and then when the water was pumped out the whatever was high and dry sitting on wooden blocks down the centerline of it and some blocks along the side to keep it from rolling over. Each sub, ship, tugboat whatever had a different bottom on it, NO they are not all smooth so it was very technical how to cut the wood blocks to keep it supported. I was never allowed to do that stuff as I didn't have the woodworking skills.
Peter Hucker wrote:Kavanagh
)
LOL!!! We used to pressure wash the subs and the midges got blasted too when they came around. Unfortunately we had to paint the subs with a paint roller so the midges couldn't be spray painted, but they did get stuck in the paint, we just kept on rolling!!
BTW it takes 7 coats of paint from bare metal to finish coat to paint a US submarine!!! They are darker on the top half than the bottom half so they tend to blend into the area around them depending on whether you are looking up at them from below or down from above at them. The only part that gets treated differently is the sonar 'dome' and it gets VERY carefully spray painted to keep the paint as thin as possible. I was a welder, plumber, carpenter and professional firefighter and EVERYONE except the cooks had to 'water blast', ie pressure wash, the subs, those things are HUGE!!! Fortunately not every inch needed cleaning or painting but every 10 days we got a new one in during 'docking season' which was Spring thru Fall every year. Fortunately for me I was only there for one year, as a single guy that was all most of us did while married guys did at least 1 1/2 years and some did more.
I never got shocked soooo much in my life from welding as when I was there....the near daily rain and constant movement of things meant alot of repairs in the rain.We had wmetal walkways to walk above the water that pooled everywhere and they needed constant rewelding to the deck. Unfortunately that meant starting the weld above the water level and then trying to keep it going down under 2 to 3 inches of water to weld the walkway back to the deck again. Since it rained all the time there was never a break to fix it solid so it was always 'good enough' until the next time.
mikey wrote:LOL!!! We used to
)
I once went camping and put the tent up, walked off for only 5 minutes, and found it covered in 950 flying ants - we counted them as we killed them, one by one by squishing them between our fingers. They were in some kind of "meet up" mode and didn't try to fly off.
Married guys get more work?
Shocked? I thought welders were about 50 volts?
If this page takes an hour to load, reduce posts per page to 20 in your settings, then the tinpot 486 Einstein uses can handle it.
Quote:Peter Hucker
)
No ours were 220/240 volts and then since we only used stick welders we changed the amps as needed with a dial on the front of the machines.
mikey wrote:No ours were
)
The only one I used was a 3kW 240V input (plugged into a standard UK socket - you can't do that in America because of your 120V systems with less power!), but with a huge transformer to give out 50 volts at a higher amperage. Not sure if that was for safety or to provide a higher current. The best way to start a good arc is with DC, but I assume all welders rectify the AC from the mains.
I'm wondering if you're related to the Russian youtube people, Kreosan. I can't find the video now, but they were welding by simply using a direct connection from the mains! They ended up melting the plug. An African guy did it better, he put a bucket of salt water in series to limit the current, and he could adjust the current by changing the gap of the electrodes in the water.
If this page takes an hour to load, reduce posts per page to 20 in your settings, then the tinpot 486 Einstein uses can handle it.
Peter Hucker wrote: mikey
)
Umm NO to all of that!!
Our welders in the Navy looked alot like this one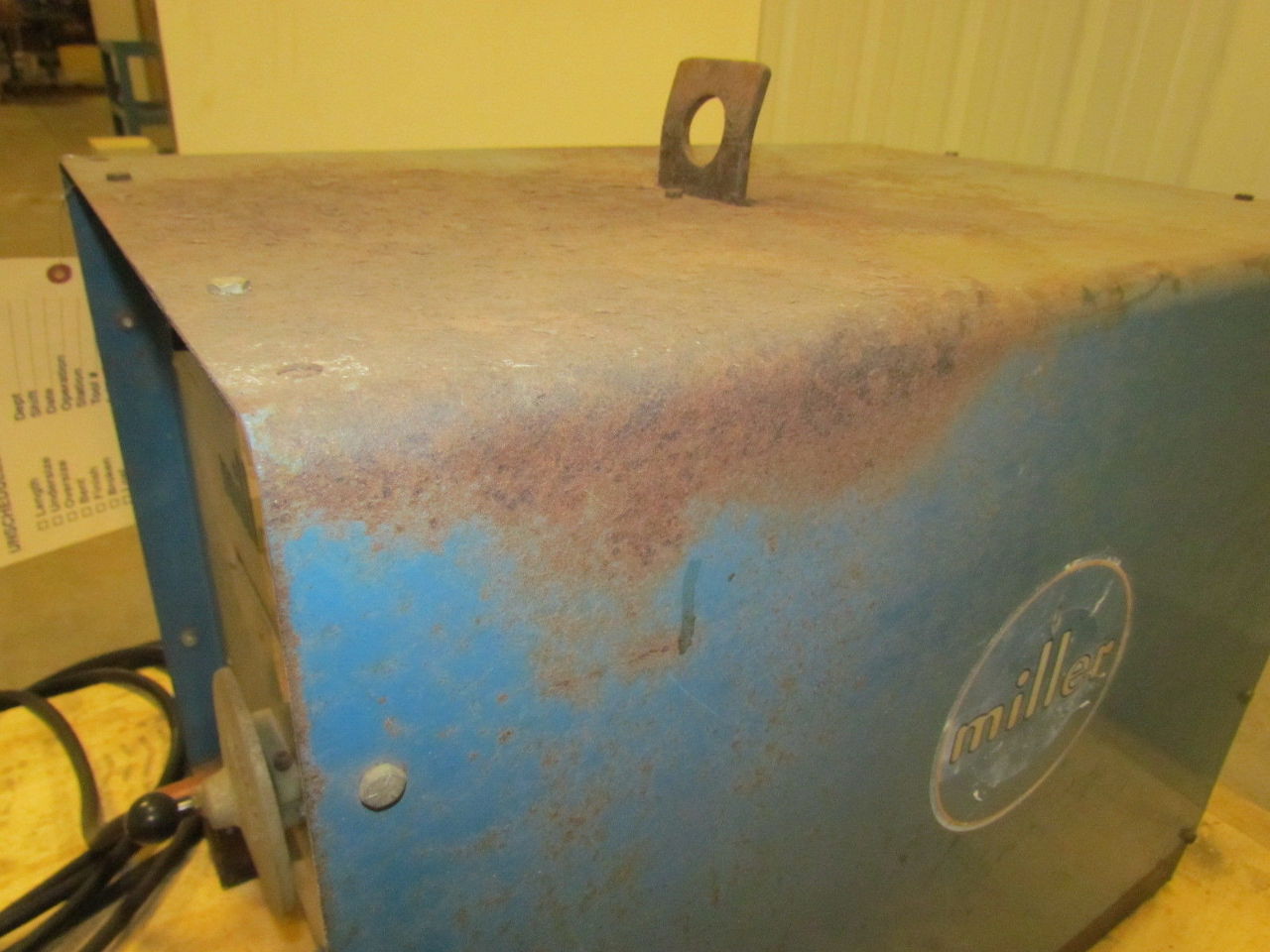
mikey wrote:Our welders in
)
This page suggests it's up to 80 volts on the output when open circuit. The one I had I measured at about 50V. I can't remember if it was DC or AC. DC apparently gives you a stronger weld.
If this page takes an hour to load, reduce posts per page to 20 in your settings, then the tinpot 486 Einstein uses can handle it.
Peter Hucker wrote: mikey
)
I have no clue but remember we had to crank it up the longer the leads were, ie being close to the welder itself or having to run wires 200 feet away and also based the material we were welding. Sometimes we cranked it waaaay down and used a 2nd welding rod as filler material when we had to fill a gap of several inches in cases where they didn't want to make a filler piece of metal. I had to fill a gap of more than 4 inches one night, yes I started after 4pm and didn't finish until after 7am the next morning. It was about 2 feet long going around a corner on an exhaust pipe. They needed to run the diesel engine starting at 8am so I did make it but it took FOREVER!!! AND it did NOT leak which was VERY important as the place where the engine was was under 40 feet of water in a pontoon with people in it when it ran. The engine ran the pumps to pump the water out of the 'wingwalls' when we went down to let the subs etc in and then when the water was pumped out the whatever was high and dry sitting on wooden blocks down the centerline of it and some blocks along the side to keep it from rolling over. Each sub, ship, tugboat whatever had a different bottom on it, NO they are not all smooth so it was very technical how to cut the wood blocks to keep it supported. I was never allowed to do that stuff as I didn't have the woodworking skills.